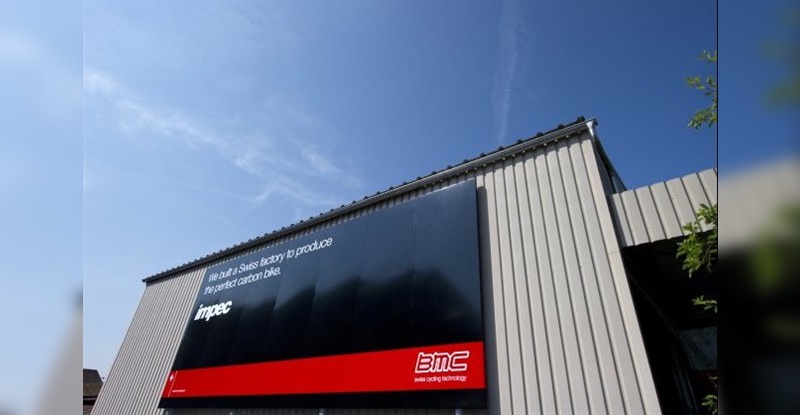
Automatisierter Rahmenbau in der Schweiz
BMC baut Hightech-Rahmenfabrik am Stammsitz Grenchen
Seit Anfang Juli läuft die serielle Fertigung von Carbon-Rahmen in der eigenen Fabrik, gleich neben dem BMC-Hauptgebäude. Das Besondere daran ist der hohe Automatisierungsgrad: Praktisch alle Abläufe von der einzelnen Carbonfaser zum Rahmenrohr und vom unbehandelten Rohr zum fertigen, lackierten Rahmen werden von Fertigungsrobotern ausgeführt. „Pro Schicht arbeiten nur gerade acht Leute in der Produktionshalle“, sagt BMC Brand Manager Markus Eggimann, der die Entwicklung und den Aufbau der Fabrik während den letzten fünf Jahren betreut hat.
Fehlerquelle Mensch ausgeklammert
Als größten Vorteil der neuen Produktion nennt Eggimann die totale Kontrolle über alle Produktionsabläufe und den fertigen Rahmen: „Dank der computergesteuerten Fertigung können wir darauf zählen, dass jeder Rahmen exakt nach unseren Plänen gebaut ist. Eine Serienstreuung, wie sie im herkömmlichen Carbonrahmenbau durch die Handarbeit entstehen können, gibt es nicht“. Ohne die großzügige Unterstützung des Unternehmers Andy Rihs wäre das nicht möglich gewesen: Der Alleininhaber von BMC hat zusätzlich zu seinen bisherigen Investitionen 40 Millionen CHF (ca. 31 Millionen Euro) für die Entwicklung und den Aufbau der automatischen Rahmenproduktion zur Verfügung gestellt.
In sieben Stationen entsteht in der Hightech-Fabrik aus einzelnen Carbonfasern der fertige Fahrradrahmen. Im ersten Arbeitsschritt werden die einzelnen Fasern zu einem Schlauch verwoben. Deren Ausrichtung und Dichte bestimmt der digitale Bauplan auf dem Trägerelement, das den fertigen Strumpf weiter zur zweiten Station transportiert. Dort wird das Harz hinzugefügt und der Strumpf zu Rohr gebacken. Gemäß Eggimann war dieser Prozess die größte Herausforderung bei der Entwicklung der automatischen Produktion. Weil es bisher noch nichts Vergleichbares gab, mussten die Abläufe komplett neu ausgedacht werden, was insgesamt drei Jahre mehr Zeit in Anspruch nahm als ursprünglich geplant. Dafür konnte BMC nun die einzigartige Technik zum Patent anmelden.
Präzision steigert Effizienz
In der dritten Station werden die Rohre mit einer Diamantfräse zugeschnitten. Auch dies geschieht, ohne dass ein Mensch Hand anlegen muss. Laut Eggimann sind die fertigen Rohre so präzise vorbereitet, dass sie nicht mehr nachbearbeitet werden müssen. Gleich nebenan fertigt die vierte Maschine Muffen und Ausfallenden im Spritzgrussverfahren. Durch die Computersteuerung gelingt es BMC, die kurzen Carbonfasern im Kunststoff für zusätzliche Stabilität belastungsgerecht auszurichten.
Bevor die einzelnen Rahmenteile zusammengebaut werden, werden sie einzeln lackiert. Es überrascht kaum noch, dass BMC auch diesen Arbeitsschritt praktisch vollständig automatisiert hat. Erst wenn die Logos im Tampondruckverfahren auf den fertig lackierten Teile angebracht werden, kommt wieder die menschliche Arbeitskraft ins Spiel. Weitere Arbeiter kommen zum Zug, um die einzelnen Rahmenteile zusammen zu stecken, bevor sie ein weiterer Roboter zusammenklebt.
Lückenlose Kontrolle
Zum Schluss werden die Rahmen noch geprüft: „Jeder Rahmen, der in den Verkauf gelangt, hat einen statischen Test durchlaufen. Die darin gemessenen Daten speichern wir zusammen mit allen Werten aus der Produktion“, sagt Markus Eggimann. Die Testmaschinen nutzt auch das Entwicklungsteam, das seine neuen Räume Tür an Tür zur Produktionshalle bezogen hat. „Dank der kurzen Wege können wir die angestrebte Qualität sicherstellen“, erklärt Eggimann. Ein weiterer Vorteil ergibt sich aus in der flexiblen Produktionsplanung: „Mit unserer eigenen Fabrik in der Schweiz können wir rasch auf Nachfrageveränderungen reagieren, gefragte Größen rasch nachproduzieren und neue Farbtrends blitzschnell umsetzen. Verzögerungen durch enge Zeitfenster bei Auftragsherstellern und lange Transportwege sind kein Thema mehr“. Weitere Vorteile bringt die eigene Produktion in der Kalkulation: „Weil wir die gesamte Wertschöpfung im Haus haben, sind wir weniger stark den Schwankungen von Wechselkursen, Transport- und Arbeitskosten ausgeliefert“, ergänzt Markus Eggimann. Preiswerter Rahmen herstellen kann BMC mit der automatisierten Produktion allerdings nicht – noch nicht, merkt Eggimann an: „Wir sind überzeugt, dass die Lohnkosten in Asien weiter stark steigen werden, und dadurch handgefertigte Carbonrahmen massiv teurer werden“.
Erstes Model Impec
Die ersten „swiss made“-Rahmen baut BMC für das neue Edel-Rennrad Impec (Selbstbewusst abgeleitet vom englischen „impeccable“: makellos). Auch wenn die Optik zu einem Teil von der Produktionsweise bestimmt wird, ist das Rad unverkennbar im BMC-Design gehalten. Die Profis des eigenen Rennteams nutzen diese Räder bereits während der laufenden Tour de France. Ab September sollen sie bei ausgewählten Händlern gekauft werden können. Das Impec kommt in der sportlichen „Race Fit“-Geometrie und der moderateren „Performance Fit“-Variante in jeweils fünf Rahmengrößen, drei unterschiedlichen Sattelstützen und zwei Farbvarianten auf den Markt. Jede Version bietet BMC im Baukastensystem wahlweise mit den Topgruppen von Shimano, Sram oder Campagnolo an, einzelne Rahmensets werden nicht verkauft. Als Gesamtgewicht peilt BMC den von der UCI für Rennen erlassenen Grenzwert von 6,8 Kilo an, das Set aus Rahmen, Gabel, Steuersatz und Stütze soll in einer mittleren Größe bei 1790 Gramm liegen. Als Qualitätsausweis gewährt BMC für das Impac lebenslange Garantie – was nicht nach EU-Recht 10 Jahre bedeutet, sondern wortwörtlich zu verstehen ist und ohne Fahrergewichtslimite auch für den Renneinsatz gilt, wie Eggimann betont.
Mittelfristig will BMC mit der eigenen Fertigung nicht nur das oberste Rennradsegment bedienen: „Mit unseren Swiss-made Bikes wollen wir ein breiteres Publikum ansprechen. Dazu gehört, dass wir die neue Technik künftig auch in tieferen Preislagen und anderen Segmenten, zum Beispiel bei Mountainbikes oder Urban Lifestye Bikes anbieten werden“, sagt Eggimann. Die Kapazitäten dafür sind vorhanden: Bis zu 25'000 Rahmen kann BMC in der Schweizer Rahmenfabrik jährlich herstellen.
Verknüpfte Firmen abonnieren
für unsere Abonnenten sichtbar.