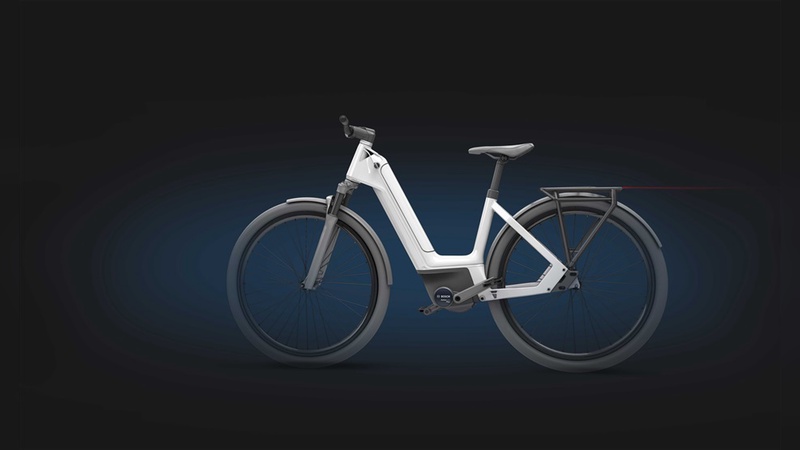
Österreichisch-deutsche Kooperation
Europäische Rahmenproduktion im Spritzgussverfahren bald serienreif?
„Ab Dezember werden die ersten Fahrradrahmen aus der Maschine fallen und nach ausgiebiger Test- bzw. Prüfphase fokussieren wir dessen Verkauf. Das primäre Ziel ist aber sicherlich, sich als hochwertiger Zulieferer für OEM´s zu platzieren“, erklärt Dr. Umut Cakmak, Geschäftsführer von Plastic Innovation und Postdoc am Institut für Polymere Product Engineering an der Johannes Kepler Universität Linz. Neben viel schnelleren Herstell- bzw. Zykluszeiten, den kürzeren Wegen und dadurch verkürzten Lieferzeiten hebt der Doktor für Kunststofftechnik und experimentelle Physik die „erheblich größere Designfreiheit und die Möglichkeiten zur Funktionsintegration“ hervor. Dies ermöglicht ein spezielles Spritzgussverfahren zur „Hohlkörperherstellung“ für Fahrradrahmen. Dafür wird ein geschlossenes Spritzgusswerkzeug komplett mit Kunststoff gefüllt. Während das Bauteil über die Werkzeugwandung außen abkühlt, hat der Kunststoff im Inneren eine Temperatur von über 200° Celsius, ist homogen und „fließfähig“. Mithilfe von einem separat angesteuerten Fluiddruck wird der Kunststoff aus dem Bauteilinneren verdrängt und so ein geschlossener Hohlkörper mit einer besonders hohen Torsionssteifigkeit geschaffen. Mit dieser Sondertechnologie wurden bisher beispielsweise Medienleitungen im Motorraum, Griff vom Maxi Cosi oder der Motorsäge sowie Dachrelings von Autos hergestellt.
Als Material verwenden die Hersteller voll recycle- und wiederverwertbare thermoplastische Composites und reduzieren so den CO2-Ausstoß nach eigenen Angaben um über 50 Prozent gegenüber Stahl- und Aluminiumrahmen. Hierfür wurde das Unternehmen 2017 mit dem Greenstart vom Klima- und Energiefond des österreichischen Umweltministeriums ausgezeichnet. Beim German Innovation Award´19 haben sie kürzlich Gold gewonnen.
Erklärtes Ziel der deutsch-österreichischen Kooperation: Die Wertschöpfungskette für hochwertige Bikerahmen wieder zurück nach Europa zu bringen. Die Produktionskapazitäten von bis zu 1.000 Fahrradrahmen pro Tag vom gleichen Modell sollen es möglich machen. Die österreichische Plastic Innovation bleibt Innovationsbüro mit eindeutigen Fokus Produkt- und Verfahrensentwicklung, der deutsche Partner Velosione GmbH mit Produktionsstätte in Schmiedefeld/Thüringen präsentiert sich im Markt als Fahrradrahmenzulieferer für die OEMs.
Weitere Informationen über die innovative Technologie sowie ein Imagevideo findet man auf http://www.plasticinnovation.at . Auch Velosione hat einen eigenen Webauftritt .
für unsere Abonnenten sichtbar.