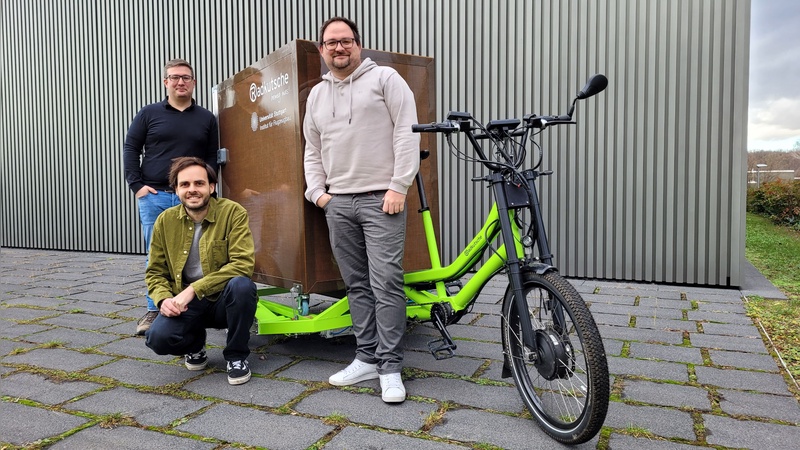
Naturfaserverbundwerkstoff spart Emissionen:
Stuttgarter Leichtbau am Lastenrad
Das Team um Klaus Heudorfer, Mathias Engelfried und Dominique Bergmann hat ein neues Herstellungsverfahren entwickelt. Mit diesem könnten Naturfaserverbundwerkstoffe zu einer nachhaltigen, sicheren und stabilen Alternative im Leichtbau werden. Leichtbauteile aus Aluminium, Glasfaser- oder Carbonfaserverbundwerkstoffen haben mitunter den Nachteil, dass sie unter hohem Energieeinsatz entstehen und sich schwer oder gar nicht recyclen lassen. So verschlechtere sich die Umweltbilanz emissionsarmer Mobilitätslösungen, argumentiert das dreiköpfige Team vom Institut für Flugzeugbau an der Universität Stuttgart. Diesen Problemen ließe sich mit der Innovation aus Flachsfasern und Bio-Polymeren Abhilfe schaffen. Naturfaserverbundwerkstoffe sind an sich zwar keine Weltneuheit. Besonders ist aber das Imprägnierverfahren, mit dem Heudorfer, Engelfried und Bergmann die hygroskopischen Flachsfasern vor Feuchtigkeit schützen. „Wir können energieintensive Leichtbaumaterialen durch einen biobasierten Werkstoff ersetzen und so im gesamten Lebenszyklus des Produkts deutlich CO2 einsparen", erklärt Klaus Heudorfer.
Kunststoffe haben die angehenden Gründer aus dem Produkt komplett verbannt. „Unser Prozess erlaubt eine effiziente Herstellung von Naturfaserverstärkten Kunststoffen NFK mit besseren mechanischen Eigenschaften als viele andere Produktionsverfahren", sagt Mathias Engelfried. Diese mechanischen Eigenschaften können sich durchaus sehen lassen. Bezogen auf das eingesetzte Gewicht ist die Steifigkeit des Naturfaserverbundwerkstoffs besser als bei Glasfaserkunststoff (GFK). Die Festigkeit sei bei gut optimiertem GFK etwas höher, bei günstigerem GFK etwas schlechter als bei der neuen Alternative aus Naturmaterial. Da das Material umweltschonender recyclebar ist als Aluminium oder Glasfaserverbundwerkstoffe, denken die Gründer bereits über Wiederverwertungskreisläufe nach.
Grundsteine für Firmengründung
Der Innovationscampus Mobilität der Zukunft, unterstützt das Team im Rahmen seines Early Ride Programms und eines Transferprojekts dabei, die Bemühungen rund um den Werkstoff aus der Forschung in ein Unternehmen zu überführen. Die Universität Stuttgart, genauer der Innovationscampus Mobilität, unterstützt das Transferprojekt nun in einem Accelerator-Programm dabei, die Bemühungen rund um den Werkstoff aus der Forschung in ein Unternehmen zu überführen. Entstehen soll ein skalierbarer industrieller Prozess. „Die nächste Herausforderung für uns ist es, unseren Prozess so weiterzuentwickeln, dass wir die Anforderungen der unterschiedlichen Branchen erreichen können", sagt Dominique Bergmann. Vor der Firmengründung wollen sich die drei Forscher noch auf ein Gründerstipendium bewerben, das die nötigen Mittel für eine funktionierende Prozesskette erbringen soll. Der aktuelle Plan lautet, im September des kommenden Jahres eine erste Fertigungsanlage zu haben, die die bisherige Laboranlage ersetzt.
Demonstrator mit Radkutsche
Um Praxiserfahrungen zu sammeln, ist das Stuttgarter Team auf den Lastenradhersteller Radkutsche zugegangen und hat für diesen eine Transportbox aus dem neuen Material angefertigt. Es gebe bereits Pläne, an diese Zusammenarbeit anzuknüpfen, verraten die angehenden Gründer. Der Demonstrator auf der Radkutsche soll zeigen, was möglich ist. Einsatzmöglichkeiten sehen die drei Forscher auch bei Innenraumteilen von Bussen, Cockpitverkleidungen oder Sitzschalen von Autos und sogar Windkraftanlagen.
Für die Fahrradbranche dürfte das Material besonders für flächige Teile, wie die Wannen von Lastenrädern interessant sein. Theoretisch ließe sich das Material auch für Rahmenteile einsetzen. An die mechanischen Eigenschaften von Carbon kommt es allerdings nicht heran. Das Stuttgarter Team ist zwar noch ein paar Schritte von der Serienfertigung entfernt, zeigt sich aber schon jetzt offen für Kooperationen. Prototypen lassen sich bereits realisieren.
für unsere Abonnenten sichtbar.