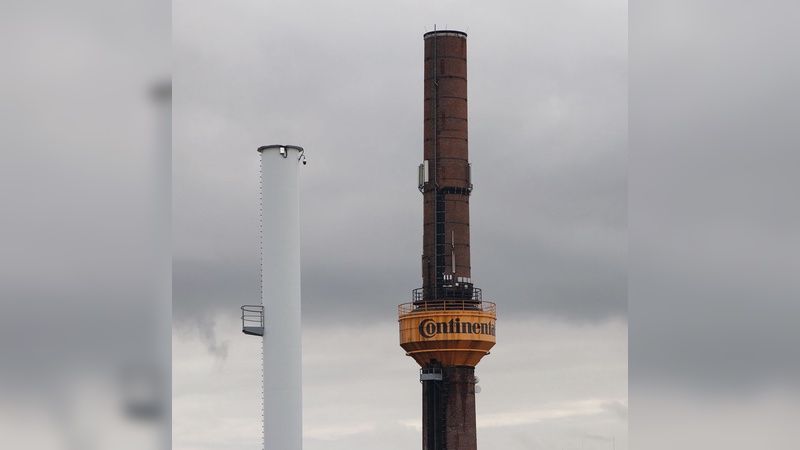
Porträt // Continental Fahrradreifen
Weltkonzern mit Fahrradwurzeln
Genau hier ist er, der Ort, um den sich sprichwörtlich alles dreht. Wo riesige Maschinen in langen Reihen heiße Ware produzieren. Entsprechend warm ist es hier drin, trotz des verregneten Herbsttags. Alle paar Sekunden hört man ein Klacken, und mit lautem Zischen öffnet eine der »Backformen« in den Reihen ihren Deckel, ein Arbeiter kommt herbei und zieht einen frischgebackenen Bike-Reifen von der Form. Glänzend und heiß, streng nach Gummi riechend. Der Mitarbeiter macht den ersten Qualitätscheck und der Pneu segelt mit gekonnt lässigem Schwung auf einen der nebenstehenden Transporttrolleys.
Gute Basis im Weltkonzern
Der Weg dahin ist länger, als man denkt. Am Anfang steht die Entwicklung des Reifens, die unter anderem auch im HPTC, im High Performance Technology Center in Korbach startet, nur ein paar Hallen vom Vulkanisieren entfernt. In der Lobby des Gebäudes präsentiert man ein Mercedes-Flaggschiff von AMG. Continental ist einer der größten Konzerne weltweit im Segment Autoreifen und Automotive. Die Reifenabteilung macht ein Viertel des Umsatzes aus.
»Die Continental-Werke in Korbach stellen ein ganzes Stadtviertel dar«, sagt Sarah Hohmann-Spohr von der Kommunikationsabteilung, Abteilung Zweiradreifen. »350.000 nach und nach gewachsene Quadratmeter.« Auf den Straßen dieses Viertels herrscht reger Staplerverkehr. Rein geht’s für einen Rundgang am Conti-orangefarbenen Pförtnerhaus, auf dem Weg zu den Fahrradreifen-Hallen ist das Unternehmens-Wahrzeichen, der Schornstein mit der Conti-Banderole, in Sichtweite.
Mit der Karkasse, also dem Gewebe, das den Reifen in Form hält, fängt der Produktionsweg des Reifens an. Sie ist hier bereits kalandriert, das bedeutet, von großen Maschinen in eine dünne Gummidecke eingebettet. Die breiten Karkassenballen werden auf die notwendigen Maße für die Weiterverarbeitung zugeschnitten. Das erledigen panzergroße Maschinen und Mitarbeiter, die häufig in den Ablauf eingreifen. Drei- oder viermal wird die Karkasse als »Hülle« des Reifens gewickelt. Das Gewebe dafür ist diagonal geschnitten, was die Komplexität bei der Berechnung des Materials erhöht, aber dem Reifen seine Stabilität gibt. Man kann sich das wie bei einem mehrmals kreuz und quer gewickelten Lenkerband vorstellen. Je feiner das Gewebe selbst, desto leichter rollt der Pneu. So haben die schnellen Rennradreifen GP 5000 bei Conti 330 TPI, also 330 Fäden pro Zoll, einfache Trainingsreifen 180. Für günstige Einstiegsreifen im MTB-Bereich reichen 84 TPI.
Auch der Wulstkern, der den Reifen auf der Felge hält, wird bei Conti hergestellt. Er ist entweder aus einem mehrfach gewickelten Stahldraht oder, für Faltreifen, aus Aramid-Fäden.
Rezepte in geheimen Kochbüchern
Der heikelste Bestandteil ist die Gummimischung aus Kautschuk, Ruß und einigen Hundert Zutaten für die Laufflächen. Sie ist bei jedem Hersteller streng geheim. Wie sie hergestellt wird, zeigt der Rundgang vor Ort nicht, wohl aber das Rohmaterial. Das Grundmaterial ist ein faseriges, grau meliertes, einige Zentimeter dickes und etwa 40 Zentimeter breites, formbares Band. Dieses wird in Extrudern, die etwa wie ein Fleischwolf arbeiten, zum gürtelbreiten Streifen geformt. »Hier gibt es natürlich besondere Herausforderungen«, erklärt Alexander Hänke, Produktmanager Mountainbike, zum oft zitierten Wollmilchsau-Faktor des Reifens. »Einerseits soll der Laufstreifen robust und möglichst durchstichsicher sein. Er soll aber auch gut haften und leicht rollen und womöglich auf einen speziellen Einsatzbereich ausgerichtet sein.« Bei Conti schwört man auf die hauseigene »Black-Chili«-Rezeptur, eine geheime Gummimischung, die je nach Einsatzbereich leicht abgeändert wird. Die jeweiligen Profile im MTB-Bereich sind ohnehin eine Wissenschaft für sich, hier zählt bei der Entwicklung neuer Pneus vor allem Erfahrung.
Der noch glatte Laufstreifen, darunter eine Pannenschutzeinlage aus Vectran, die zwei Wulstkerne, zwei Nesselbänder (schmale Gummistreifen, die den Reifen am Rand vor Abnutzung durch das Felgenhorn schützen), sowie die gummierte Karkasse werden schließlich verheiratet. Ein Mitarbeiter legt auf eine rotierende Trommel mit Reifendurchmesser am Kopf einer großen Maschine alle Einzelteile nacheinander auf und längt sie passend ab. Die Trommel ist verstellbar, sodass unterschiedlichste Rohreifen gefertigt werden können. Zuletzt kommt der Laufstreifen mittig auf dieses Arrangement. So entsteht der Grünling, also der Rohreifen. Er enthält schon alle Bestandteile des Reifens, die hier aufgrund des Materials ohne Weiteres zusammenkleben. »Das ist einer der vielen Arbeitsplätze, bei denen es auf Erfahrung und Sorgfalt ankommt«, betont Hohmann-Spohr beim Rundgang. Erst jetzt merkt der Besucher: Ja, hier herrscht tatsächlich viel aufwendige Handarbeit.
Vor zehn Jahren schon hatte Conti mit einer Made-in-Germany-Kampagne und authentischen Fotos vieler Mitarbeiter einen Marketing-Coup gelandet und Sympathien bei Handel und Kunden eingeheimst. Die halbe Belegschaft lernte man dabei kennen. So wurde Qualität aus Deutschland mit einem Schmunzeln kommuniziert.
Kommt der Grünling von der Trommel, geht’s in die eingangs vorgestellte Vulkanisierhalle. Wie vorgebackene Brötchen werden hier die Reifen fertig gegart. Was sie vor dem Backofen noch nicht haben, ist das Profil. Das bekommen sie von der Form, in die sie gebettet werden und die dann mit dem enormen Druck von 15 bar bei 170 Grad Celsius auf das Gummi-Allerlei einwirkt. Wie präzise diese Formen gearbeitet sein müssen und welchen Aufwand die Werkzeugmacher hier betreiben müssen, kann man sich gut vorstellen, wenn man sich beispielsweise die aufwendigen MTB-Reifenprofile vor Augen führt.
Das Bike lernt vom Auto. Und umgekehrt.
Die Synergie-Effekte in der Entwicklung werden von allen Beteiligten geschätzt. »Wir haben hier enorme Expertise in allen Bereichen«, sagt Jan-Niklas Jünger, Produktmanager Rennrad-Reifen. »Ganze Abteilungen, die sich mit Gummimischungen auskennen wie niemand sonst. Überall herrscht Teamwork. Es gibt keinen Reifen, der nur weitgehend von einer Person entwickelt wird. Wir können natürlich viel von der Expertise der Kollegen aus dem Autosektor profitieren.«
So war das auch beim Taraxagum. Der 2019 vorgestellte Fahrradpneu wird zu einem großen Teil aus russischem Löwenzahn hergestellt. »Wir können mit diesem Rohstoff genau dieselbe Qualität erreichen wie mit dem klassischen Naturkautschuk«, erklärt Hohmann-Spohr. »Das ist eine spezielle Züchtung, die mit einfachen Böden auskommt. Das bedeutet: Wir können damit sehr nachhaltig produzieren.« Nicht nur, dass damit die Urwälder geschont werden, nachhaltig sind auch die Transportwege. Der Rohstoff für den Urban Taraxagum kommt unter anderem aus Mecklenburg-Vorpommern. Im Preis für den Endverbraucher unterscheidet der grüne Pneu sich auch kaum von Standardreifen. »Natürlich waren auch hier Synergieeffekte wesentlich«, erklärt Hohmann-Spohr. Ohne das Autoreifen-Projekt zu Taraxagum hätte es wohl keinen grünen Fahrradreifen gegeben. Der ist mittlerweile mehrfach mit Awards bedacht worden und in limitierter Stückzahl im Laden angekommen, während es für den nachhaltigen Autoreifen von Conti noch etwas Zeit braucht.
Von Anfang an groß gedacht
Das alles lag noch in weiter Ferne, als das erste Conti-Werk 1871 in Hannover gebaut wurde. Bereits als Aktiengesellschaft gegründet, stellte man zunächst Massivbereifungen für Fahrräder und Kutschen her. 1892 folgte dann der Schritt zu den Pneumatics, den Luftreifen, eine Alleinstellung in Deutschland. In den Zwanzigerjahren übernahm man im Rahmen einer größeren Fusion das Gummiwerk in Korbach, das Louis Peter, ebenfalls ein Reifen-Pionier, 1907 gegründet hatte. Natürlich gab es auch hier dunkle Jahre. Wie viele große Unternehmen war Conti in Zeiten des Nationalsozialismus ein wichtiger Zulieferer der NS-Rüstungswirtschaft. Aber der Konzern hat die Offenheit, die unrühmliche Zeit als Teil seiner Geschichte anzuerkennen. Im August 2020 wurde eine von Conti in Auftrag gegebene umfangreiche Studie eines Historikers dazu veröffentlicht, die weit ins Detail geht.
1950 hat Conti 13.500 Beschäftigte im Hannoveraner Stammwerk. In den 50ern und 60ern engagiert man sich viel im Rennsport, 1967 wird das Contidrom eröffnet, eine eigene Test-Rennstrecke. Zu Wirtschaftswunder-Zeiten wächst der Konzern immer mehr. Unter anderem wird die europäische Uniroyal-Reifensparte aufgekauft, bald danach kommt auch Semperit unter das orangefarbene Dach. Conti verstärkt seine Aktivitäten im Automotive-Bereich, wird dort das zweitgrößte Unternehmen weltweit. Heute gibt es 595 Konzern-Standorte in 59 Ländern, darunter ein eigenes Reifenwerk in Hefei, China, wo auch Fahrradreifen produziert werden. Außerdem gibt es dort ein Partner-Werk, das in Auftrag von Conti fertigt. In Indien produziert ebenfalls seit einigen Jahren ein Werk Conti-Fahrradreifen im Auftrag. Die Premiumreifen wie etwa die Rennrad-Ikone Grand Prix 5000 und viele andere gibt’s aber nur Made in Germany und nur aus Korbach.
Mobilität in allen Facetten
Der Konzern ist in viele innovative Mobilitätsbereiche involviert, auch wenn sein E-Bike-Antrieb nur ein kurzes Gastspiel in der Realität hatte. Beispiele sind weitreichende Entwicklungen im autonomen Fahren oder der in Serie produzierte Abbiege-Assistent für Lkws, der hoffentlich bald konsequent eingesetzt wird. Dennoch ist die aktuelle Situation für die Automotive-Sparte naturgemäß schwierig. Die Krise der Autobranche setzt dem Unternehmen zu. Weltweit sollen bis zu 30.000 Angestellte entlassen werden. Conti kann sich von den allgemeinen Entwicklungen so wenig frei machen wie andere.
Da ist es gut, dass die Fahrradbranche boomt wie nie. »Wir stehen gerade sehr gut da«, sagt Jünger. Durch die Produktion im Inland hatte man im ersten Corona-Lockdown Anfang 2020 einen entscheidenden Vorteil. So war der Lieferketten-Stress der anderen ein Katalysator für die Nachfrage bei Conti. Die Produktion in Korbach wurde deutlich erhöht. »Wir sind hier mengenmäßig kaum limitiert«, erklärt der Rennrad-Spezialist. Das war auch gut für die zahlreichen OEM-Kunden von Canyon über Rose bis Stevens oder Scott. Besondere Aushängeschilder sind Reifendesign-Entwicklungen für kleine, aber edle Partner aus der Branche wie Schindelhauer. Mittlerweile fertigt man auch die blauen Reifen für den Abo-Verleiher Swapfiets. Gerade wurde das Reifenprogramm in Richtung Falträder (wie etwa ein 16-Zöller für das Brompton) und Cargobikes erweitert. Spezielle E-Bike-Pneus gibt es bei Conti schon länger, mittlerweile auch eine Version des Contact-Urban-Reifens mit Zulassung für S-Pedelecs. »Wir versuchen, für alle Bereiche, die das Fahrradfahren vorantreibt, eine Produktlösung zu finden«, meint Jünger. Aber: »Egal, worum es geht, wir wollen nie nur den schnellsten Reifen oder den langlebigsten haben. Es geht uns um die ideale Komplettfunktion für den jeweiligen Bereich, möglichst breit angelegt.« So muss der neue Cargobike-Reifen nicht nur eine Achslast von 120 Kilogramm aushalten, er soll auch langlebig sein und schnell laufen.
Offene Kundenkommunikation
Seit gut zwei Jahren ist Conti breit in Social-Media-Kanälen unterwegs. »So bleiben wir nachhaltig mit dem Kunden in Kontakt«, so MTB-Mann Hänke. Außerdem arbeitet man aktiv mit Influencern zusammen. »Fahrradfahren ist einfach Lifestyle, das drückt etwas über dein Selbstverständnis aus«, erklärt Hohmann-Spohr. Im Urbanen und auch im MTB-Sektor will Conti die Marke noch deutlich stärken. »Da gibt es noch viele Geschichten zu erzählen«, ergänzt Hohmann-Spohr. Geschichten, die vielleicht auch mit den World-Tour-Teams im Rennrad-Bereich zu tun haben, traditionell tritt Continental hier sehr aktiv als Sponsor auf. Man sitzt aber auch fest im MTB-Sattel: Der kultige britische Downhill-Clan Atherton wird von Conti unterstützt. Die zentrale Geschichte dürfte aber auch in Zukunft bleiben, wie die die »Backformen« in Korbach mit einem Zischen einen neuen Pneu Made in Germany freigeben. //
Verknüpfte Firmen abonnieren
für unsere Abonnenten sichtbar.