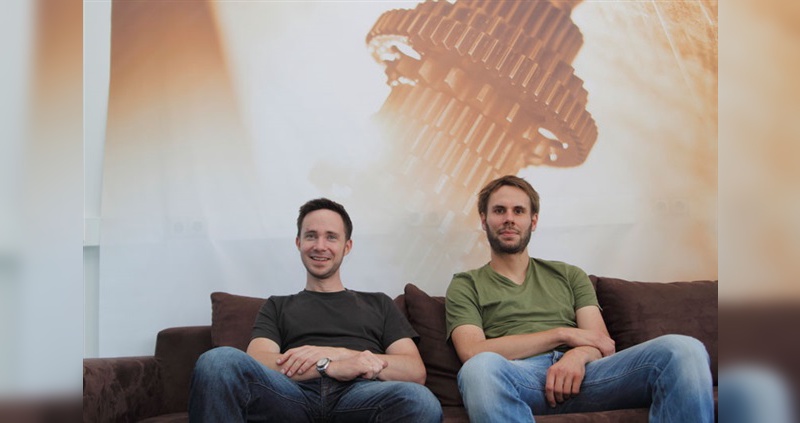
Portrait - Pinion
Das Beste oder nichts
Der Boden im Südwesten Deutschlands scheint reich gesegnet mit Genie-Dünger. Unternehmen wie Bosch, Daimler-Benz und Porsche entstanden um die Ecke, einige kleine, besonders feine Unternehmen aus der Bike-Branche sind heute auch nicht weit entfernt. Gesteigertes Elitebewusstsein kommt im Verhalten der beiden jungen Chefs von Pinion trotzdem angenehm wenig zum Ausdruck. Im schlicht-praktischen Gewerbebau in Denkendorf bei Stuttgart trifft man weder auf Hipster oder betont geniale Freaks, sondern schlicht auf zwei sympathische Männer in den Dreißigern ohne Allüren, die vor allem eins ausstrahlen: Ruhe. Vielleicht deshalb, weil sie wissen, was sie wollen.
Michael Schmitz und Christoph Lermen haben 2006 angefangen, das Pinion-Getriebe P1.18 zu entwickeln und zu bauen. Acht Jahre später lassen namhafte und große Firmen wie Koga, Stevens, die Winora-Gruppe oder KTM, aber auch feine Highend-Hersteller wie Idworx oder Velotraum mit dem Getriebe aus Denkendorf schalten. Und das, obwohl die Pinion-Option das Rad für den Verbraucher im Schnitt etwa 1500 Euro teurer macht als dasselbe Bike mit einer Mittelklasse-Kettenschaltung. Dafür bekommt er das derzeit einzige Tretlager-Getriebe: 18 Gänge, voll gekapselt, nahezu wartungsfrei, extrem robust und durch seine schwerpunktgünstige Lage bestens für fast jede Art von Fahrradeinsatz geeignet. Im Gegensatz zum Planetengetriebe, wie es in Nabenschaltungen zum Einsatz kommt, ist es auch relativ einfach, mit einem Stirnradgetriebe wie dem P1.18 gleichmäßige Schaltstufen zu bekommen, und so übersetzt der jeweils nächste Gang des Getriebes um etwa 11,5 Prozent länger.
Von der Automobilindustrie lernen, heißt siegen lernen
Die Automotive- und die Automobilbranche besitzen weltweit enorm hohe Entwicklungsstandards und arbeiten methodisch sehr effizient. Sicher auch deshalb kommen immer wieder technisch sehr durchdachte Bike-Produkte von Unternehmen, die ursprünglich im Automobil- und Fahrzeugbau unterwegs waren. Beispiel: Magura mit dem Dauerbrenner hydraulische Felgenbremse oder auch Rohloffs Speedhub 500/14. Auch die Pinion-Macher kommen aus dieser Ecke. Michael Schmitz studierte Wirtschaftsingenieurwesen KFZ-Technik, als er 2006 im Praktikum Christoph Lermen in der Prototypen-Abteilung für Motoren und Getriebe von Porsche kennenlernte. Der war Luft- und Raumfahrttechnik-Student. Beide fuhren hobbymäßig gerne Fahrrad. In ihrer Freizeit. Ein Kollege dagegen kam täglich mit dem Rad ins Werk. Eines Tages aber viel zu spät: Seine Schaltung war abgerissen. »Eine Diskussion entflammte«, so Christoph Lermen: »Warum gibt’s im Fahrradbereich kein Getriebe wie beim Auto? Eines, an dem man nie etwas machen muss, und das nicht einfach mal kaputtgehen kann, das ewig hält?« Und dabei auch noch schwerpunktgünstig liegt und somit Handling und Fahrdynamik verbessert. Nach dem Motto: Ein Ölwechsel im Jahr und gut ist’s.
Lermen und Schmitz nahmen die Diskussion ernst. Fingen an, zusammen über eine Lösung nachzudenken, investierten Zeit. Irgendwann war klar, dass sie das Problem auch wirklich praktisch lösen wollten. Doch schnell stellte sich heraus: Einfach Erfahrungen aus dem Fahrzeugbau anwenden ging nicht. Das liegt unter anderem daran, dass in den zwei Bereichen gänzlich unterschiedliche Parameter ausschlaggebend sind. Ein Automotor arbeitet hauptsächlich in einem Drehzahlbereich von 2000 bis 5000 Umdrehungen, während ein Radler zwischen 30 und 100 Umdrehungen auf die Tretlagerachse bringt. Problem: Das maximale Drehmoment kann mit etwa 250 Newtonmeter trotzdem bei beiden gleich sein. »Die Berechnungsmodelle vom Auto passen also überhaupt nicht aufs Fahrrad«, so Lermen. »Bei klassischer Umrechnung wäre unser Getriebe viel größer geworden und hätte mindestens acht Kilo gewogen – statt jetzt 2,7.« Problemanalyse und Abarbeitung, so hieß die Beschäftigung mit dem Thema im ersten Jahr. »Wir haben weniger die direkten praktischen Erfahrungen übertragen als vielmehr die Herangehensweise an die aufkommenden Probleme«, erzählt Schmitz.
Ein Patent auf die Tretlagerschaltung haben sie nicht – solche Getriebe gab es mit zwei oder drei Gängen schon in der Frühzeit des Fahrradbaus. Aber es gibt zehn Patentanmeldungen über Kniffe und Tricks, das Ganze kleiner und robuster zu halten.
2008 wurde Lermen klar, dass Studium, Arbeit als Werksstudent und Getriebeentwickler doch etwas zu viel Zeit von einem einzelnen Menschen einfordern. Schmitz, der mittlerweile sein Studium abgeschlossen hatte, und Lermen sagten Porsche auf Wiedersehen, ungeachtet der guten Aussichten, die das Unternehmen bot, und gründeten 2008 Pinion. Kontakte zur Fahrradbranche gab es so gut wie keine. »Das war nicht nur von Nachteil«, meint Schmitz schmunzelnd: »Die Branche ist ja teilweise etwas eingefahren. Natürlich mussten wir einen Umweg machen, lernen, wie die Branche tickt. Aber vielleicht hätten wir das Projekt als Insider irgendwann auch fallen gelassen. Denn es ist uns heute klar, dass wir zunächst von praktisch allen Seiten gehört hätten: Das kann doch nichts werden.« Keine Klientel, viel zu teuer, zu schwer, da machen die Rahmenbauer nicht mit – tatsächlich hat man die Einwände der Branche fast im Ohr, wenn man sich die Szenerie überlegt.
»Anfang 2009 war der Getriebeaufbau im Prinzip ganz klar, und von da ab wurde nur noch versucht, es einfacher, robuster zu machen. Und einfacher herzustellen«, ergänzt Schmitz.
Ideen haben ist gut. Dran bleiben noch besser.
Firmengründung? Was sich groß anhört, war eine Notwendigkeit: »Wir mussten einen Prototypen bauen. Als wir den Preis für einen Satz Zahnräder sahen, fiel uns die Kinnlade runter.« Ein Investor musste her. Und dafür braucht ein Unternehmen nun mal einfach einen rechtlichen Status. So entstand Pinion. Der Name: englisch für Antriebszahnrad. Ursprünglich für das erste Produkt, die 18-Gang-Nabe, gedacht, wurde es zum Firmennamen umdeklariert – »er war so einfach, kurz und griffig«, freut sich Lermen.
Mit dem ersten Investor hatten sie Pech: Er kam aus der Automotive-Branche und da waren diese Jahre bekanntlich keine guten Jahre. Er sprang ab. Ein zweiter, selbst Physiker und fasziniert von der Pinion-Idee, fand sich 2009. Der Prototyp konnte gebaut werden, es ging weiter. »Zu der Zeit stellt man fest, dass die Idee bei so einer Entwicklung eigentlich die kleinere Herausforderung ist«, erzählt Lermen, »schwieriger ist es, dran zu bleiben.«
Bei diesem Gespräch sitzen wir in Ihrem dritten Domizil: im Denkendorfer Gewerbebau hat Pinion 2012 die erste und zweite Etage bezogen. Unten sind die Büros und die Produktion, oben der Prototypenbau, Labor und Lager. Insgesamt etwa 1000 Quadratmeter. Es gibt fast nur Glaswände, und es wird relativ großzügig mit Platz umgegangen, was den ganzen Betrieb sehr freundlich und aufgeräumt erscheinen lässt. Es herrscht konzentrierte Betriebsamkeit, aber keine Hektik.
Handarbeit made in Germany
Das liegt auch daran, dass der Geräuschpegel nicht von klassischem Lärm automatischer Maschinen beherrscht wird. Nahezu alles wird hier in Handarbeit gemacht: Das Getriebe wird in einzelnen Baugruppen gefertigt. Es gibt zum Beispiel die Baugruppe Griff/Bedienungseinheit, die bestückte Eingangswelle des Getriebes oder die bestückte Schaltwelle. Die klassische Werkbankmontage. Zur Sicherung des Flow gibt es für jede Baugruppe Verantwortliche im Pinion-Team. Die Größe der Aufträge liegen bei 100 bis 200 Stück. Und: Jede der Montagekräfte kann jeden Arbeitsschritt ausführen. Diese Struktur heißt mitnichten, dass es hier altbacken zugeht. Es geht vor allem sehr genau zu. Alles, was gemessen werden kann, wird bei der Montage elektronisch überwacht. Sei es der Einpressdruck von Lagern in ihre Schalen oder etwaige andere Messschritte. »Das sind meist einfache Messungen«, so Schmitz, »doch sie helfen, Qualität von Anfang an zu sichern.« Und die muss bei einem Produkt im High-End-Bereich natürlich maximal sein. Jedes einzelne Getriebe wird zum Schluss getestet: Es kommt in ein Fahrrad auf Rolle mit Schnellspann-Aufnahme für das P1.18 und wird rauf- und runtergeschaltet. Auch auf Dichtigkeit des Gehäuses wird geprüft: Jedes P 1.18 wird bei 80 Grad Celsius »gebacken« um zu testen, ob Öl austritt.
Der größte Stolz von Schmitz und Lermen ist aber der etwa fünf Meter lange Getriebeprüfstand, der letztendlich auch den Ausschlag gab, sich das neue Domizil in Denkendorf zu suchen. An dieser Maschine wird in der Mitte das Getriebe eingespannt. »Rechts ist der Antrieb, links quasi die Straße – ein Generator. Antriebs- und abtriebsseitig werden die Drehmomente gemessen.« So lassen sich also auch Wirkungsgrade ermitteln – beim P1.18 liegen sie laut Pinion im Schnitt bei etwa 97 Prozent. Mithilfe dieser Maschine können Einzelteile im Gesamtzusammenhang getestet werden. »Wir sind in der Lage, nahezu jedes einzelne wichtige Teil auszutauschen und dann eingebaut zu überprüfen«, so Lermen. Übrigens werden fast alle 140 Einzelteile des Getriebes im Radius von etwa 200 Kilometern hergestellt. Nur die Kurbel und einige Kleinteile kommen aus Asien.
Innovationen sind gut fürs Image
War es ein weiter Weg bis nach Denkendorf? Wie reagierten die Fahrradhersteller auf den Neuzugang? 2010 standen die beiden Pinion-Gründer erstmals auf der Eurobike – und konnten damit eine ganze Branche überraschen. Ausgerechnet das Nachrichtenmagazin Spiegel wusste als einziges Medium einige Tage vorher von der Schalt-Revolution in Spe. Pinion konnte auf der Messe Räder einiger kleiner, feiner Bikehersteller mit dem P1.18 zeigen. Nicolai und Tout Terrain gehörten zu den ersten Partnern. »Wir hatten keine Probleme, Interesse zu wecken«, erzählt Lermen. »Ein technisch so wichtiges Detail wie die Schaltung kann faszinieren. Die Hemmschwelle für den Bike-Anbieter ist da relativ gering, denn wer Innovation, die auch den Endkunden faszinieren kann, unterstützt, tut auch was für sein Image. Auch bei den Teile-Zulieferern aus der Automotive-Branche sind wir zum Schluss hin offene Türen eingerannt«, sagt er. »In dieser Branche denkt man ohnehin oft in anderen Dimensionen.« Ein weiterer Grund für die einfach zu handelnden Geschäftskontakte dürfte sein, dass man sich vor allem in Krisenzeiten im Automotive-Bereich gerne an zukunftsorientierten Unternehmen andockt und sich damit Zugang zu anderen Industriezweigen verschafft – auch wenn das vorerst, von den Stückzahlen her gesehen, eigentlich wenig effizient ist. Auch hier weiß man: Die Ausgaben der Verbraucher für Fahrräder steigen von Jahr zu Jahr. Die Tendenz: Der Verbraucher will hohe Qualität und gibt immer mehr für sein Hobby- oder Alltagsgefährt aus. »Allerdings«, ergänzt Lermen, »spürten wir es schnell, als es der Automobilindustrie wieder besser ging: Die Lieferzeiten unserer Zulieferer wurden plötzlich wesentlich länger.«
Zurück zu den Radherstellern: »Wir haben zu anfangs 20 Unternehmen angefragt. 16 waren dabei«, erzählt Schmitz stolz. »Kleine Hersteller haben die Möglichkeit gesehen, sich technisch und innovativ von der Masse abzuheben«. Die größeren brauchten noch eine Weile, bis sie das Potenzial erkannten. Heute fahren auch Marktgrößen wie Koga, Stevens, KTM oder die Winora-Gruppe auf dem Pinion-Zug mit. »Da mussten wir erst Vertrauen aufbauen, zeigen, dass das P1.18 kein Strohfeuer ist.« Dabei machte man es den Herstellern leicht: Der erste Entwurf, bei dem der Fahrradrahmen Teil des Getriebegehäuses war, wurde schnell verworfen, da klar war, dass man sich damit viel zu sehr von der Arbeit der Rahmenbauer abhängig machte. Außerdem mussten die Hersteller damit einen sehr großen Eigenanteil leisten. Deshalb entschied man sich bei Pinion für eine »Brücke«. Das Alu-Schmiedeteil, das für geringes Geld an die Hersteller verkauft wird, ist sehr einfach an vorhandene Rahmengeometrien anpassbar. Es wird mit den Rahmenrohren verschweißt und nimmt die Schaltung auf. »Das ist für uns ein ganz wichtiges Bauteil«, erzählt Schmitz, »ein Produkt, das den Rahmenbauern erleichtert, in die Pinion-Partnerschaft einzusteigen. Ein Türöffner bei großen Firmen.«
Doch auch seit dem ersten Eurobike-Auftritt vor vier Jahren ging es nicht im ICE-Tempo weiter: Die genannten Probleme mit Zulieferern funkten den Getriebemachern dazwischen und mussten geklärt werden, und das zog sich etwas hin. Seit 2012 läuft nun die Serienproduktion in Denkendorf. Und seitdem geht’s rasant bergauf. Im Vergleich zum letzten Jahr haben sich die Jahres-Produktionszahlen deutlich erhöht, sie liegen jetzt im mittleren einstelligen Tausender-Bereich, gibt Pinion an. Mittlerweile schreibt man in Denkendorf bereits schwarze Zahlen.
Die Fachmedien servierten das P1.18 erwartungsgemäß als Sensation, was es aufgrund der Alleinstellungsmerkmale tatsächlich auch ist. Aber auch in den Tests der letzten Jahre wurde das Getriebe viel gelobt. Und wenn einmal nicht nur gelobt wird, wie im Fall von Trekkingbike-Chefredakteur Tom Bierl, der dem Getriebe ein mahlendes Geräusch bescheinigte, wird schnell und effizient nachgebessert – vielleicht auch etwas, was mit dieser Akkuratesse branchenintern nicht selbstverständlich ist.
Der Weg zum Systemanbieter
Die Zukunft hält einige Überraschungen bereit. Zwar ist die vor zwei Jahren gezeigte Kombi aus E-Motor und Ge‑
triebe zumindest vorübergehend ad Acta gelegt – »E-Mobilität ist derzeit ein Haifischbecken, da müssen wir nicht auch noch rein«, so Lermen. Doch auf der diesjährigen Eurobike präsentiert das Unternehmen gleich drei echte Neuerscheinungen: Die Neunfach-Schaltungen P1.9 und P.1.9 XR sowie die 12-Gang-Schaltung P1.12. Sie kommt mit 600 Prozent auf eine fast so lange Übersetzung wie das »große« Pinion, hat dabei aber Gangsprünge von etwa 17,5 Prozent, was insbesondere für den Mountainbikebereich interessant sein dürfte. Die »kleine« 9-fach-Schaltung bewegt sich im Bereich klassischer Nabenschaltungen und hat entsprechend auch eine deutlich geringere Entfaltung. Adressiert werden mit dem preisgünstigsten Pinion-Modell insbesondere hochwertige Urban- und Citybikes, während die »extended Ration« XR fast die Entfaltung der P1.18 hat, aber etwa doppelt so große Gangsprünge – ein Konzept, das vor allem für E-Bikes, aber auch Mountainbikes sehr interessant sein dürfte. »Alle diese Getriebe haben die gleiche Basistechnologie des P1.18. Das heißt, dass wir die Konstruktionen relativ einfach ableiten konnten – aus dessen Schalteinheiten«, so Schmitz. »Das System ist gut skalierbar, man muss nur beim ersten Produkt alles mitdenken«, schmunzelt er. »Alle zukünftigen Varianten müssen reinpassen. So haben wir geguckt, was man maximal realisieren kann – und dann aus diesem Konzept außerdem an Produkten rausholen kann.«
Und natürlich haben alle dieselbe Brücke als Aufnahme; man muss es den Bikeherstellern ja nicht unnötig schwer machen. Außerdem soll es eine Variante für Fatbikes geben, bei der die Kettenblatt-Aufnahme und Kurbeln weiter nach außen wandern. Das funktioniert bei allen vier Getriebevarianten.
In mittlerer Zukunft kann man sich bei Pinion sogar kundenspezifische Lösungen vorstellen. Vom Hersteller eines Produkts zum Systemanbieter – das ist auch das Ziel der Pinion-Macher für die nächsten Jahre. Sie sind schon gut dabei.
Verknüpfte Firmen abonnieren
für unsere Abonnenten sichtbar.