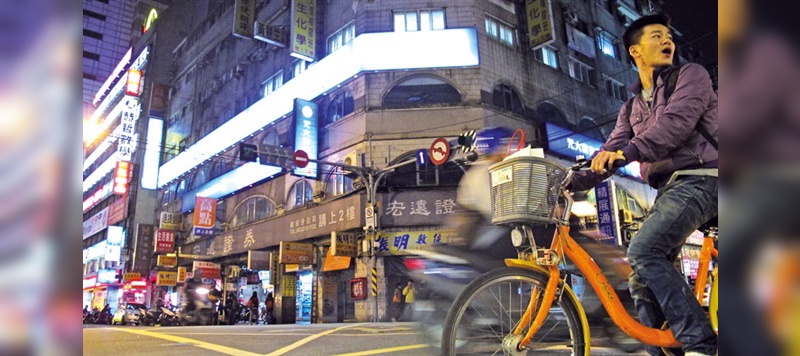
Report - Fertigung in Asien
Produzieren in Fernost
Der Grund für Magura und DT Swiss nach Taiwan und dort in die Industriemetropole Taichung zu ziehen, ist schnell erklärt: Im Umkreis von einer Autostunde befindet sich hier ein Großteil der weltweiten Produktion hochwertiger Fahrräder und Fahrradteile. Es sind nicht nur die Produktions-Giganten Merida und Giant, die hier auch für andere renommierten Marken fertigen, sondern unzählige weitere Rahmenbauer, Montagebetriebe, Komponenten-Hersteller und mit ihnen all die hochspezialisierten Vorlieferanten. Will man als Hersteller seine Produkte nicht nur in homöopathischen Mengen an die Endkonsumenten verkaufen, sondern auch als OEM-Lieferant eine Rolle spielen, so hat es entscheidende Vorteile, in Taiwan vor Ort zu sein.
Magura in Asien
Magura eröffnete 2002 das erste Büro in Taichung, genau 9439.2 Kilometer vom schwäbischen Firmensitz Bad Urach entfernt, wie man als Besucher präzise erfährt. Das Büro diente erst nur zu Repräsentationszwecken. Bald schon wurden dort jedoch die ersten Bremsanlagen für OEM-Kunden zwischengelagert. Etwas später begann man in dem Büro die Hydraulik-Leitungen der Bremssysteme genau auf Kundenwunsch abzustimmen, um den OEMs einen besseren Service bieten zu können. Ein erster Umzug stand 2007 ins Haus. Immerhin 760 qm große Räumlichkeiten bezog das deutsch-schwäbische Unternehmen. Da auch diese bald aus allen Nähten zu platzen drohten, erfolgte 2011 ein zweiter Umzug. Auf komfortablen 5900 qm startete Magura dort im selben Jahr auch die Produktion von Federgabeln, 2012 wurden die ersten Scheibenbremsen hergestellt. Rund ein Drittel der Fläche beansprucht heute die Produktion, den Rest teilen sich Lager und Administration: Von Taichung aus steuern die Mitarbeiter auch Verkauf, Marketing, Distribution, Qualitätskontrolle von Produkten der Taiwanesischen Zulieferunternehmen sowie den Service und insbesondere auch die Ausbildung bzw. Schulung der Asiatischen Kunden und Distributoren. In Taiwan arbeiten 54 Personen für Magura. Zum Vergleich: In Bad Urach sind es ca. 400 Mitarbeiter.
2013 folgte die Zertifizierung von Magura Asia nach Iso-9004.
Geklonte Produktionsanlagen
Magura hat bei der Bremsen-Produktion eine wohl durchdachte Trennung eingeführt: In Taichung werden jene OEM-Scheibenbremsen hergestellt, welche in Fernost verbaut werden. In Bad Urach fertigt für die europäischen Produzenten und den Nachrüstmarkt. So ist man sehr nahe am Produzenten dran und kann eine hohe Flexibilität und kurze Lieferzeiten bieten. Dass es wenig sinnvoll ist, Bremsen in Europa zu produzieren, diese für die Assemblage nach Fernost zu liefern, damit sie montiert am Fahrrad wieder zurück nach Europa verschifft werden, weiß Magura aus der eigenen Vergangenheit. Die geringeren Produktionskosten spielen da nicht einmal eine solch entscheidende Rolle: Einerseits ist ein großer Teil der Produktion automatisiert, anderseits ist Taiwan mit einem Durchschnittslohn von circa 1200 Euro im Monat weit davon entfernt ein Billiglohnland zu sein. Hier liegt Taiwan irgendwo im gesamteuropäischen Mittelfeld, leicht unter jenem von Portugal, aber leicht über demjenigen von Tschechien.
Gemäß Magura macht die Asiatische Produktion 10 % der gesamten Bremsenproduktion aus. Gefertigt werden in Taichung ausschließlich Scheibenbremsen, die bei den Europäischen Herstellern beliebten Felgenbremsen stammen ohne Ausnahme aus dem deutschen Werk. Nicht ganz so differenziert ist die Strategie bei den Federgabeln: In Deutschland entwickelt erfolgt die Endmontage der zugelieferten Teile im Werk in Taichung. Daneben produziert Magura in Taiwan zusammen mit diversen Partner-Betrieben noch einige Motorradteile (Lenker) und Elektronik-Komponenten.
Auch wenn die Produktionsstandorte Taichung und Bad Urach fast 10.000 Kilometer voneinander entfernt liegen: Die Produktionslinien sind an beiden Standorten identisch. Es kommen die gleichen Maschinen zum Einsatz, die gleichen Grundstoffe, der gleiche Produktionsablauf.
Wird eine neue Produktelinie eingeführt, so wird zunächst im Mutterwerk der Fertigungsprozess entwickelt, getestet und perfektioniert. Bei Magura Asia entsteht anschließend ein Klon der Produktionsanlage. So unterscheiden sich die Bremsen aus Taiwanesischer Produktion in Aussehen, Funktion und Qualität nicht von den Produkten »Made in Germany«. Einzig die Serien-Nummer verrät den Ursprung der Bremse.
Und bei der Produktionshalle in Taichung bestätigt sich das oben beschriebene Bild: Wüsste man es beim Besuch vor Ort nicht besser, man könnte auf den ersten Blick nicht darauf schließen, sich in Asien zu befinden. Alle Räumlichkeiten sind sehr hell und auffällig sauber. Der Boden ist so blank geputzt, dass man ohne Probleme darauf essen könnte. Die Air-Condition leistet ganze Arbeit und verbannt das subtropischen Klima nach draußen. Dass wir uns in Taiwan befinden, verraten nur die chinesischen Schriftzeichen an Maschinen und Materialbehältern – sowie die Mitarbeiter.
Apropos Sauberkeit: Um möglichst keine Verschmutzung in den Produktionsprozess einzuschleppen, gibt es mehrere Schmutzschleusen. Alle angelieferten und kontrollierten Teile werden für die Montage aus Karton- in Kunststoffkisten verpackt. Die einzelnen Räume verfügen über ein spezielles Zutritts-System. Damit können Mitarbeiter gewisse Räume nicht so ohne Weiteres betreten. Gerade in Hinblick auf Verschmutzung und ihren kostspielige Folgen ist dies sicherlich ein sinnvoller Ansatz. Gleichwohl wird nach dem Toyota-Produktions-System gearbeitet: Alle Abläufe sind rückverfolgbar bis zum Grundmaterial.
Bernd Herrmann leitet Magura Asia und führt die Produktion. Für ihn sind die Mitarbeiter der Schlüssel zum Erfolg. Die meisten kämen aus der nächsten Umgebung und würden sich sehr stark mit dem Betrieb identifizieren, sagt Herrmann. Die Arbeitswoche ist nach deutschem Vorbild angelegt: Sie hat fünf Arbeitstage, an denen jeweils acht Stunden gearbeitet wird.
Typisch asiatisch ist eine gewisse Einheitlichkeit bei der Kleidung: Bei unserem Besuch fällt auf, dass alle Mitarbeiter Magura-T-Shirts tragen. An allen Montagen ist dies für alle Mitarbeiter Pflicht. An den anderen Wochentagen kann jeder frei wählen.
Zufriedene Mitarbeiter: Diese Zielsetzung seht ganz oben bei Magura Asia. Demensprechend wird hier auch viel investiert – so zum Beispiel in eine Air-Condition in allen Räumen, was im feucht-heißen Sommer Taichungs für angenehmere Arbeitsbedingungen sorgt.
Magura ist mit dem Standort Taiwan für die Asien-Geschäfte sehr zufrieden. Von staatlicher Seite herrsche viel Stabilität, sodass langfristig geplant werden könne. Auch die Mentalität der Mitarbeiter bezeichnet Herrmann als sehr zuverlässig und kooperativ.
DT Swiss Taiwan
Auch DT Swiss hat bereits vor zehn Jahren seine erste Niederlassung in Taiwan eröffnet. Vor sechs Jahren wurde ein bestehender Industriebau übernommen und man begann vor Ort die ersten Produkte zu fertigen. Unterdessen ist ein weiteres Fabrikationsgebäude dazugekommen. Die Belegschaft ist auf 150 Mit‑
arbeiter angewachsen. Davon sind 95 % Taiwanesen, geführt wird die Asien-Niederlassung durch eine Schweizer Crew.
Gerade am Beispiel von Speichen, noch immer ein zentraler Geschäftsbereich von DT Swiss, welche in den unterschiedlichsten Ausführungen, Längen und Farben nachgefragt werden, zeigt, welche Standortsvorteile die Produktion vor Ort bringt. All die verschiedenen Ausführungen könnten kaum in genügender Zahl gelagert werden, um auch einer kurzfristigen Nachfrage eines Fahrradproduzenten in Asien nachzukommen. Die ökonomisch (und ökologisch) vertretbare Lieferung aus der Schweiz per Containerschiff würde viel zu lange dauern.
So fertigt DT Swiss in Taichung ungefähr 10 % seiner Speichen. Darunter sind die auch nicht konifizierten Speichen, die ausschließlich aus Taichung stammen. Allerdings heißt das nicht, dass nicht mit derselben Präzision wie in der Schweiz gefertigt würde: Es kommen exakt dieselben Maschinen wie in Biel zum Einsatz, die mit identischem Rohmaterial aus Schweden gefüttert werden. Und auch für das Einfärben der schwarzen Speichen vertraut man in Taichung denselben Prozessen wie in Biel. Bei den konifizierten »Competition«-Speichen reisen die endverdickten Speichenrohlinge aus Biel an. Vor Ort werden diese dann auf die richtige Länge zugeschnitten, mit dem Speichenkopf versehen, gebogen und das Gewinde wird gerollt. Wenig überraschend: Auch hier findet man dieselben Maschinen wie in Biel. Qualität steht über allem. Neben den Speichen entstehen in Taiwan auch Naben und Schnellspanner. Aus einem separaten Gebäude rollen Laufräder. Diese sind jedoch praktisch ausschließlich für asiatischen Fahrradproduzenten be‑
stimmt. Neben der Fertigung koordinieren die Mitarbeiter in Taichung auch die Belieferung der OEM-Kunden und die Zulieferung der taiwanesischen Vorlieferanten und leisten den Service für den asiatischen Raum. Während unseres Besuchs in Taichung fand eine Schulung für asiatische Velohändler für DT-Produkte statt.
Neben dem Produktionsstandort in Taichung hat DT Swiss eine weitere Fertigungsstätte in Polen, die europäische Industriekunden mit Laufrädern versorgt. Die Niederlassung in den USA ist auf Distribution und Service für den nordamerikanischen Markt spezialisiert. Im Hauptsitz in Biel sitzen die Konzernleitung, das Engineering und Marketing.
Auch wenn die Niederlassungen von DT Swiss über den ganzen Erdball verstreut liegen, sind sie trotzdem miteinander verbunden. So steuert ein einheitliches System von Biel aus beispielsweise die EDV für alle DT-Swiss-Niederlassungen weltweit.
Wettbewerb um Arbeitskräfte
Trotz aller Internationalität hat sich DT Swiss auch eine gewisse Heimatverbundenheit erhalten: Die Kerntechnologien und Spezialitäten, wie zum Beispiel das Konifizierungs-Verfahren für Speichen oder die Produktion der legendären 240er-Naben, bleiben weiterhin in der Schweiz. Gemäß Bernd Böckmann, Verkaufsleiter bei DT Swiss, soll das auch in Zukunft so bleiben. Jedoch gibt Böckmann zu, dass dies eine Herausforderung darstelle. Nicht primär das Lohnniveau, wie man vielleicht vorschnell schließen könnte, sondern die Verfügbarkeit von qualifizierten Arbeitskräften im Großraum Biel, sei eine große Schwierigkeit. DT Swiss steht im Wettbewerb um die besten Arbeitskräfte in Konkurrenz zur zahlungskräftigen Uhrenindustrie.
Gute Mitarbeiter zu finden ist auch für Urs Keller, Werksleiter in Taichung, eine Herausforderung. Der Arbeitsmarkt in Taiwan ist ausgetrocknet, die Arbeitslosenquote liegt unter 4 %. Auch hier sind andere Branchen vor Ort, die bessere Löhne zahlen können als die Fahrradindustrie. Neue Wege müssen eingeschlagen werden. Insbesondere junge Taiwanesen sind vermehrt auf Arbeitsuche. Der Grund: Der akademische Bildungsweg in Taiwan ist sehr populär und üblich. Jedoch verfügen die jungen Arbeitssuchenden zwar meist über einen Universitätsabschluss in einer Wissenschaft, haben aber wenig praktische Kenntnisse, welche für einen Fabrikationsbetrieb von Nutzen sein könnten. Urs Keller hat daher begonnen, junge Universitätsabsolventen für die Aufgaben in der Firma auszubilden und hat dafür ein eigenes Schulungsprogramm entwickelt. So ist die DT-Niederlassung in Taichung nicht nur Herstellungs-, sondern auch Ausbildungsbetrieb.
Um die Leute behalten zu können, investiert das Unternehmen viel in die Mitarbeiterzufriedenheit. Auch bei DT sind die Arbeitsräume klimatisiert. Die Fabrik ist hell und sauber. Die Mittagsverpflegung gewährleistet eine eigene Kantine. Die Büroarbeitsplätze sind für europäische Verhältnisse zwar knapp bemessen, aber deutlich über dem asiatischen Durchschnitt. Für eine rollstuhlgängige Mitarbeiterin wurde direkt vor dem Eingang ein Parkplatz eingerichtet. An der geringen Fluktuation zeigt sich, dass die Bemühungen Früchte tragen.
für unsere Abonnenten sichtbar.