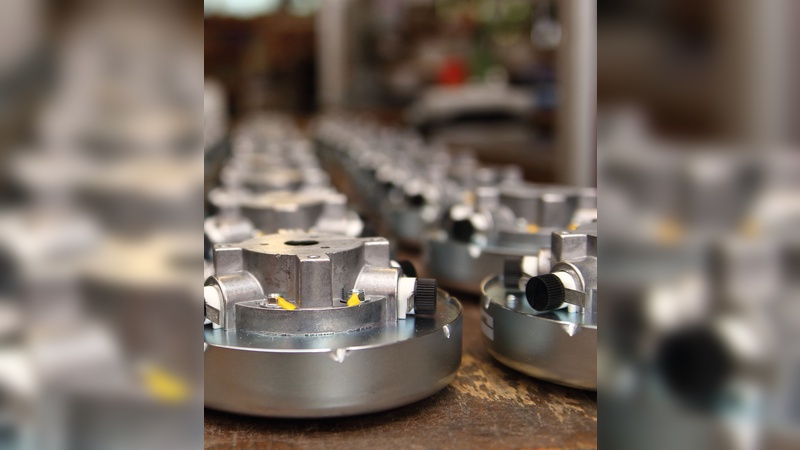
Porträt - Heinzmann
Starke Stücke aus dem Schwarzwald
Der Name dieses Unternehmens war schon damals, als sich der Elektromotor noch schüchtern in der Reha-Nische versteckte, allgegenwärtig. Aber nur für die, die den Schriftzug auch fanden. Der Hersteller verfolgte eine sehr zurückhaltende Öffentlichkeitsstrategie, obwohl man den ersten Motor fürs Rad schon 1994 entwickelt hatte. Etwas bekannter wurde Heinzmann beim Endverbraucher später mit dem unter eigenem Schriftzug gelabelten E-Bike, der Estelle. Bald gab es mit dem bürstenlosen DirectPower-Motor auch einen kräftigen Nachrüstmotor. Doch spätestens mit dem Aufkommen der Mittelmotoren wurde es stiller um den kräftigen Schwarzwälder Nabenmotor. Auch wenn das im Stammsitz niemand wörtlich sagt, dürfte die geringe Publikumsbekanntheit des Namens wohl daran liegen, dass bis vor einigen Jahren die Philosophie herrschte, »der Kunde meldet sich schon, wenn er etwas braucht.« Und heute?
Der Managing Director Electric Drives im Heinzmann-Stammsitz Schönau, Peter Mérimèche, könnte auch klassischer Musiker sein. Mit seinem etwas länger getragenen, lockigen Haar und seinem emotionalen Auftreten denkt man weniger an den Elektroingenieur als an den Kapellmeister. Wenn er hinter seinem Schreibtisch erklärt, den Zeigefinger wie einen Taktstock gestreckt, ist er kaum zu bremsen.
Auf 2000 Quadratmetern werden in Schönau im Schwarzwald heute Motoren für E-Bikes und viele andere Bereiche gebaut.
Wer weiß, dass das Unternehmen jahrzehntelang so introvertiert auftrat, dass selbst viele E-Bike-Fans bis vor Kurzem den Namen Heinzmann nie gehört hatten, entdeckt auch mit dieser Personalie, dass sich die Zeiten beim E-Motor-Pionier geändert haben müssen.
Vom Drehzahlregler zum E-Bike
1897 Gründete Max Joseph Heinzmann sein Unternehmen. Er lieferte damals vor allem mechanische Drehzahlregler, Geräte, mit denen man den Lauf von Verbrennungsmotoren kontrolliert. Anfang des 20. Jahrhunderts machte man sich damit einen guten Namen, später auch mit Produkten in anderen Industriezweigen. Motormanagement nennt man das heute. 1937 übernahm Sohn Fritz Heinzmann das Unternehmen, baute es weiter aus und verlagerte es 1946 von Dresden aus in die Nähe von Stuttgart. Nach seinem Tod 1967 übernahm Anton Gromer die Geschäftsführung und gab 1984 den Startschuss für die Entwicklung der E-Motoren und den Ausbau dieser Sparte. Auch die digitale Reglertechnik für Motoren wurde bald breit aufgestellt. 1999 gab er an den Sohn Markus Gromer weiter. Unter dessen Leitung wuchs das Unternehmen und wurde mit vielen Zukäufen nochmals breiter aufgestellt. Heute gibt es mehrere Unternehmensstandorte mit unterschiedlicher Ausrichtung. Automations- und Überwachungssysteme werden ebenso hergestellt wie Automotive-Komponenten, unter anderem auch Abgasregelsysteme, die aus Verbrennungsmotoren saubere Motoren machen. Insgesamt hat die Heinzmann-Gruppe 14 Niederlassungen, darunter acht Produktionsstandorte.
Anders als etwa bei Bosch, der auch einen riesigen Markt für Endverbraucher bedient, hatten die Heinzmann-Produkte bis vor wenigen Jahren kaum Berührungspunkt mit Endkunden. Man hatte also wenig Anlass, öffentlich präsent zu sein, wichtig war das Netzwerk innerhalb der Industriezweige. In der heutigen Zeit, in der mediale Präsenz so wichtig ist, wird das aktiv geändert. Unter anderem mit dem starken Helden des E-Bike-Booms, dem Lastenrad.
Der Lastenrad-Boom bringt öffentliche Wahrnehmung.
Das führt zum aktuellen Kernprodukt, der Sparte Electric und dem CargoPower-Motor. Auch er hat bereits eine Historie. 1994 entstand der erste E-Bike-Motor bei Heinzmann, ein Bürstenläufer oder bürstenbehafteter Motor, so die Nomenklatur bei Heinzmann. Ab 2004 kam der weiterentwickelte Classic Motor unter anderem bei der Deutschen Post zum Einsatz. Von den 10.000 Rädern für die Briefzustellung sind heute noch viele in Gebrauch.
In der Fahrradwerkstatt werden vor allem Radnaben-Motoren in Lastenräder von Kunden eingespeicht.
Ein Update folgte 2014 mit dem bürstenlosen DirectPower-Motor, der mit doppelt so hoher, nämlich 100 Kilo Zuladung, umgehen konnte. Das DirectPower-System kam zudem als robuster und starker Nachrüstmotor mit 60 Newtonmetern auf den Markt. Der Durchbruch, wenn auch für den Endverbraucher immer noch im Schatten der Wahrnehmung, kam ab 2018 mit dem CargoPower-System. Die Vorteile, erklärt Gerrit Kaupp, Operations Manager, liegen darin, dass durch das integrierte Planetengetriebe die Drehzahlen gesenkt werden, was sich unter anderem in der verringerten Lautstärke und höheren Robustheit ausdrückt. Die Schrägverzahnung sorgt für einen leisen Lauf. Ein Clou ist die Öllagerung des gesamten Motors. »Die Skepsis, dass Nabenmotoren bei Belastung schnell erhitzen, ist damit hinfällig«, so Kaupp. Natürlich ist das deutlich aufwendiger in der Konstruktion als bei vielen Konkurrenten. Doch laut Heinzmann lohnt es sich genauso wie das »Deckel-/Topf-Prinzip«. Das Motorgehäuse kann mit sechs Schrauben geöffnet werden, sodass man direkt an den Motor selbst kommt. Das Rad muss also nicht ausgespeicht und die Nabe an der Mittel-Verklebung aufgebrochen werden, wie es bei manchen Mitbewerbern der Fall ist. Die interne Kommunikation der Systemmodule erfolgt über Can-Bus. »Und der Verschleiß des Antriebs ist, gerade beim Lastenrad, deutlich unter dem der Mittelmotoren.« Die Verkaufszahlen des Motors liegen heute bereits im zweistelligen Tausender-Bereich pro Jahr, »in Kürze werden sie im dreistelligen Tausender liegen«, schiebt Mérimèche nach.
Der Renner ist heute das CargoTwinPower-System für die boomenden Lasten-Dreiräder. Es besteht aus zwei Motoren für Hinter- oder Vorderachse, den zwei Steuerungseinheiten, der Akkutechnik sowie dem Kabelbaum. Die Motoren liefern je 125 Watt Nennleistung ab, sodass sie in die Pedelec-Normen erfüllen, bringen zusammen aber bis zu 220 Newtonmeter Drehmoment für bis zu 500 Kilogramm Systemgewicht der Lastenräder.
Doppelte Power, Custom Made in Germany
»Den großen Unterschied macht aber unsere kundenspezifische Anpassung«, erklärt später Christoph Riedel, Vertriebschef Electric Drives. »Wenn ein Cargobike-Hersteller wie etwa der Kunde Radkutsche von uns ein System kaufen will, bekommt er immer ein perfekt auf seinen Anspruch zugeschnittenes Produkt.« Denn alle Eckdaten des Kundenfahrzeugs, von der Geometrie bis hin zum Gewicht und einer gewünschten Rekuperations-Möglichkeit, werden mithilfe einer Matrix abgecheckt.
Kundenspezifische Ausstattung gibt’s für die Motorsteuerung (oben) und im Aufbau des Motors. (unten)
15 Seiten lang werden Parameter der Architektur des Kundenrads abgefragt, die Daten werden in ein Programm eingegeben und ein System, das bis hin zu den einzelnen Kabellängen definiert ist, entsteht virtuell. Andere Hersteller haben einfache, fixe Systeme. »Die sagen ›friss oder stirb‹«, so Riedel. Lediglich die Software wird hier vom Hersteller angepasst.
Wie viel Einfluss diese Parameter auf das Produkt haben, erlebt man auch in der Heinzmann-Produktion vor Ort. Stolz ist man hier unter anderem auf den Nadelwickler, der hinter Glasscheiben rasend schnell seinen Job macht und die genau berechneten Wicklungen der Spulen in den Rotor setzt, ähnlich einer automatischen Nähmaschine. Vieles ist hier aber, auch wegen der individuellen Zusammenstellung des Systems, Handarbeit. Das geht von der Verkabelung der einzelnen Spulen im Motor über die Ablängung der Kabel bis hin zu den Einstellungen der Software. Alles kann für den Kunden individuell unterschiedlich sein.
»Zweimal im Jahr gibt es ein Software-Update für die Kunden«, so Riedel. Denn natürlich wird auch die Software weiterentwickelt. Auf dem 2000 Quadratmeter-Areal in der Halle für E-Motoren-Produktion gibt es derzeit flexible Linien für den CargoPower-Motor wie für den DirectDrive. Daneben werden beispielsweise E-Motoren gebaut, die in Schiffen oder in automatischen Fahrzeugen zum Einsatz kommen. Beim E-Bike montiert man im One-Piece-Flow-Prinzip. Ein einzelner Mitarbeiter komplettiert einen großen Teil eines Systems. Aber auch Arbeitsteilung ist möglich, »je nach Auftragslage, -art und Dringlichkeit«, so Gerrit Krupp beim Rundgang durch die Produktionshalle. Auch der Controller wird hier per Hand vervollständigt und mit dem Motor verbandelt. Die kundenspezifische Software wird aufgespielt und kontrolliert. Jedes einzelne System durchläuft schließlich die End-of-Line-Qualitätskontrolle. Und natürlich ist auch hinterher die Entstehung jedes einzelnen Systems in jedem Punkt nachvollziehbar.
E-Mobilität in der Entwicklung
Um immer auf Höhe der Zeit zu bleiben, wird nicht nur en détail weiterentwickelt. »Das geht auch bis in die Forschung«, sagt Alexander Herm, Entwicklungsleiter im Bereich Electric Drives. Die Universität Freiburg etwa ist ein Projektpartner. Der Anteil der Ingenieure im Stammsitz in Schönau liegt bei rund einem Viertel, eine eindrucksvolle Zahl. Die Zukunft berge noch einige Aufgaben für alle, meint Herm. »Natürlich suchen wir aktiv nach neuen Materialien, in Anbetracht von steigenden Rohstoffpreisen und Materialverknappung und besonders der Umweltbelastungen mancher heutiger Stoffe. Da gibt es in nächster Zeit noch viel tun.«
Letzteres gilt auch für die Energielieferanten. Auch Wasserstoff ist hier schon stark im Rennen. »Wir haben beispielsweise ein landwirtschaftliches Fahrzeug mit Wasserstoff-Antrieb.« Wasserstoff auch für den Sektor Mobilität? Da ist der Entwicklungsleiter skeptisch. »Dazu muss die Energiespeicherung erst nachhaltig gelöst werden.« In der produzierenden Industrie wird die Motivation, von Verbrennungs- auf E-Motoren umzurüsten, ebenfalls sichtbar. »Die Umwelt-, Geräusch- und Schadstoff-Belastung, da gibt’s viele Gründe.«
Mit neuer Offenheit zu neuem Erfolg
»Natürlich haben wir immer schon sehr kundenorientiert gearbeitet«, erklärt Managing Director Mérimèche später. Aber etwas hat sich in den letzten Jahren drastisch geändert. Man gehe seit einigen Jahren proaktiv auf den Kunden zu. »Wir haben klar die Präsenz in den sozialen Medien, etwa Linked-In und Youtube, mit großem Erfolg gesteigert«, erklärt Mérimèche. »Hier werden neben den OEM-Kunden auch die Endverbraucher angesprochen.«
Das wird in Zukunft vor allem auch den Chainless Drive betreffen, ein Antriebssystem, das Heinzmann auf der Eurobike 2021 vorstellen wird. Hier erzeugt ein Generator beim Pedalieren Strom, der im Akku zwischengespeichert und bei Bedarf an die Nabenmotoren abgegeben wird. Kette oder Riemen fallen weg. So entsteht ein sauberer, wartungsfreier und je nach Energiezufuhr nachhaltiger Antrieb für Lastenräder, aber langfristig sicher auch für andere E-Bikes. Entsprechend sieht man den Antrieb, den man mit Schaeffler als Partner entwickelte, als Kern für den zukünftigen Erfolg im E-Bike-Sektor. »Das ist sicherlich eine der wichtigsten Lösungen, sowohl für den Endverbraucher als auch für das Vermiet- und Flottengeschäft.« In diesem Punkt sieht man sich im Zusammenklang mit den CargoPower- und CargoTwinPower-Systemen einer großen Zukunft entgegenrollen, schließlich war die Deutsche Post nur der Anfang des Flottenbooms. Hersteller und Unternehmen wie Amazon, Draisin, Ono, Radkutsche, Rytle oder Bp-Mobility sind einige Beispiele der vielen Partner von Heinzmann. Der Bereich Electric Drive kann in den letzten drei Jahren eine Umsatzverdreifachung aufweisen. Dabei sind 80 Prozent der Antriebe, wie etwa beim Partner Citkar, TwinPower-Systeme. Das Modell Loadster, ein bereits erfolgreiches Berliner Kabinen-Pedelec-Lastenrad, wird bald schon mit dem kettenlosen Antrieb zu haben sein. Derzeit wird die Software in puncto Ansprechverhalten und natürliches Trittgefühl feingetunt.
Als wichtigste Umsetzung im Bereich Service-Produkte sieht Mérimèche für die nächste Zukunft die Cloud-basierte Wartung. Ab 2022 soll diese Fernwartung in großem Stil für die Heinzmann-Kunden möglich sein. »Ein Meilenstein«, ist Mérimèche überzeugt.
»Wir sind immer noch im Wandel, das ist ein andauernder Prozess.«
Peter Mérimèche, Managing Director Electric Drives
Aber »der Wandel des Unternehmens findet auch intern statt«, sagt die Marketingleiterin Martina Denhard-Aisenpreis, die seit 16 Jahren im Unternehmen ist. Dazu haben auch die heute sehr flachen Hierarchien und kurze Entscheidungswege beigetragen. »Und wir sind gut durch die Pandemie gekommen, konnten die Zeit intern auch sehr gut nutzen.« So wurde zum Beispiel der Markenauftritt überarbeitet. »Wir sind immer noch im Wandel, das ist ein andauernder Prozess«, ergänzt Mérimèche. In diesem entstanden auch die regelmäßigen Shop-floor-Meetings und andere Konzepte, mit denen die Mitarbeiter aktiver in die Entscheidungsstrukturen eingebunden werden. Und das trägt Früchte. »Die Mitarbeiter nach ihrer Meinung zu fragen und ihnen auch zuzuhören, hat enorme positive Auswirkungen«, stellt der Manager fest. Grundsätzlich scheint das Arbeiten im Heinzmann-Stammhaus ohnehin Spaß zu machen. Der 90-jährige Senior-Consultant Anton Gromer ist noch heute jeden Tag im Büro.
Verknüpfte Firmen abonnieren
für unsere Abonnenten sichtbar.