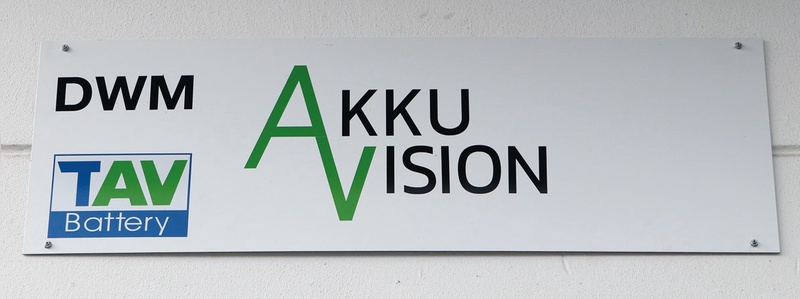
Porträt - Akku Vision
Volle Ladung made in Germany
Wir haben eine enorme Wertschöpfungstiefe«, erklärt Benjamin Hoesel, Produktionsleiter bei Akku Vision, nicht ohne Stolz, »und das ist auch sehr viel Handarbeit.« Beides überrascht in der Produktionshalle von Akku Vision. Wertschöpfungstiefe in Sachen High-End-Elektronik in Deutschland? Erwartet der Laie hier nicht vor allem Hightech-Roboterarme, die in fast menschenleeren Hallen Tag und Nacht emsig vor sich hinsurren? Stattdessen stehen hier in einer großen Halle mit ESD-Ausstattung (Electro Static Discharge, also elektrostatische Entladung) an nicht allzu langen Fertigungslinien Männer und Frauen, die unter anderem Batteriezellen in vorgefertigte Kunststoffgitter stecken. Diese sitzen wiederum in farbigen Schablonen, die sowohl die Polung der Zellen als auch deren genauen Steckplatz definieren. Es wirkt ein bisschen wie Lego: Fehler ausschließend, übersichtlich, klar.
Vom After-Market-Vertrieb zum OEM-Zulieferer
2014 übernahm der heutige Geschäftsführer Daniel Maiberger das Unternehmen E-Bike-Vision in Attendorn, den Vorgänger des Unternehmens. Eine Firma, die Ersatzakkus für E-Bikes vertrieb.
Eine kleine Halle für die Produktionslinien von 270.000 Akkus per Jahr: Das Unternehmen fertigt Akkus komplett in Deutschland.
»Maiberger gestaltete sie völlig um«, erklärt Florian Schüßler, CPO bei Akku Vision, wie das Hauptunternehmen seit 2020 heißt. Maiberger hatte bald den Fokus auf eigene Akkuentwicklung gesetzt, und er hatte eine klare Vorstellung, was er erreichen wollte: Direkt in Deutschland Ersatzakkus für die großen, gängigen Systeme entwickeln und produzieren. Diese sollten dann auch noch preiswerter sein als die Originale der großen Anbieter. Zudem sollte Akku Vision OEM-Zulieferer mit Produkten made in Germany werden.
Kurzer Durchlauf durch die Historie: 2012 bot E-Bike-Vision die erste zum Panasonic-26-Volt-System kompatible Batterie an. 2014, im Jahr der Übernahme, folgte die Batterie zum Gazelle-System, 2015 kam der Durchbruch mit der Bosch-Classic-Line-Systemkompatibilität. 2019 kamen die Akkus für Yamaha und Bosch Active und Performance Line.
»Ein großer Schritt war es nochmals zur integrierten Batterie«, so Schüßler. »Da ist vieles anders«, erklärt auch Erik Bär, COO der TAV Battery GmbH und Prokurist von Akku Vision. Auch Bärs Erfahrungen bei einem großen deutschen Batteriehersteller für E-Bikes waren sicher förderlich für die weitere Entwicklung des Unternehmens, die 2020 eingeschlagen wurde. Die TAV gehört heute zum Unternehmensverbund, ein Joint-Venture mit der Triathlon Batterien GmbH, die, wie Bär sagt, »das Wachstum und die weitere Entwicklung der Akku Vision stützen kann.« Sie produziert Batterien, unter anderem für Gabelstapler und andere Nutzfahrzeuge.
Alles aus einer Hand. Auch das Wachstum
Angefangen hatte man mit zwei Mitarbeitenden, nun sind es insgesamt 72. Nach mehreren Umzügen sitzt man in einem Industriegebiet in Haibach aus den Siebzigerjahren mit den typischen, durch An- und Umbauten verwinkelten Gebäuden aus der Zeit. Kaum jemand würde vermuten, dass so viel Hightech und Know-how hinter den blechverkleideten Fassaden steckt. Auf 5000 Quadratmetern wird hier entwickelt, getestet, produziert, gelagert, vertrieben. Lediglich ein Teil der Entwicklungsabteilung ist nach wie vor bei Karlsruhe untergebracht.
Die 3D-Drucker in der Konstruktionsabteilung sind laufend damit beschäftigt, Gehäuse, Prototypen und Teile davon herzustellen.
Früher war es ein eigenes, verpartnertes Unternehmen. Die Kollegen und Kolleginnen schätzen es aber, weiter in der Nähe ihrer alten Arbeitsstätte wohnen bleiben zu können, so wurde die Abteilung nicht verlegt. Aufgekauft wurde letztes Jahr auch die jvi GmbH, ein Hardware-Bestücker. Denn die Hardware kommt heute auch von AV. Schüßler zeigt die Platinen, die die gesamte Akkusteuerung tragen. Alles darauf ist selbst entwickelt.
Der Inframe-Akku für das Bosch-System ist beispielsweise eine besonders aufwendige Entwicklung. Die Zellen sind dort aus Platzgründen gänzlich anders angeordnet als bei den anderen Bauformen, die Zellverbindungen müssen neu konstruiert werden, das Gehäuse ist nicht aus Kunststoff, sondern aus Aluminium. Die Leiterplatten haben viel weniger Platz im Inframe-Akku, der gerade zum E-Bike-Standard wird. Die aufwendige, aber konsequente Lösung von Akku Vision lautet, die Platinen auf beiden Seiten zu bestücken.
Apropos Zellen: Mittlerweile setzt man auf die neuere 21700er-Größe statt der 18650-Zelle. Diese seien inzwischen deutlich leistungsfähiger. Durch die Pandemie wurde die flächendeckende Auslieferung allerdings verzögert. »Wir sitzen da alle im gleichen Boot«, erklärt Bär, »der Riese Bosch genauso wie die kleineren Anbieter.« Bei Zellen sind alle Hersteller fast ausschließlich auf die Importe aus Asien angewiesen, es gibt nahezu keine Produkte aus Europa. »Unsere Zellen sind von zum Großteil von Samsung, LG, Panasonic, BAK, EVE«, zählt Bär auf. Aber auch der junge Kieler Hersteller Univercell ist unter den Partnern. »Wir qualifizieren die Zellen selbst, fordern von jeder neuen Zelle auf dem Markt Muster an und verifizieren ihre Daten. Standard bei der 21700 sind heute 5 Amperestunden Kapazität, aber es bildet sich gerade ein neuer Standard mit bis zu 5,8 heraus.« Wer sich hier durchsetzt, werde den Markt bestimmen.
Ersatzakkus mit Qualitätsgarantie
Natürlich sind die großen Anbieter wie Bosch und Yamaha zunächst im Fokus, wenn es um Ersatzakku-Lösungen geht: Die Bike-Absatzzahlen großer Unternehmen verursachen auch hohe Nachfragen nach Ersatzakkus. »Wir sehen uns die Produkte, zu denen wir kompatible Akkus bauen wollen, genau an. Aber wir entwickeln grundsätzlich selbst, nach unseren eigenen Vorgaben«, so Bär. »Wir gehen mit dem Reverse-Engineering Gedanken da ran. Es wird nichts kopiert. Ziel ist immer auch, ein hochqualitatives Produkt mit einer höheren Kapazität als das Original zu liefern.« So hat beispielsweise der Akku für das Bosch-Active-Line-System 720 statt 500 Wattstunden.
Die Hard- wie die Software wird von Grund auf neu konzipiert. An der mechanischen Entwicklung sitzen vier Konstrukteure. Nur Spritzguss- oder Stanzteile werden nicht von Akku Vision selbst produziert, Gleiches gilt für die Rohplatinen. Grundsätzlich sind die Akkus gelabelt, auf jeder Aftermarket-Batterie ist der E-Bike-Vision-Schriftzug zu finden. Geschäftspartner ist dabei der Fachhandel. Er kauft für den Kunden über den Internet-Shop die Batterie bei Akku Vision, genauer bei E-Bike Vision, was seit 2020 der Name der After-Market-Akkus ist. Auch Reklamationen werden logischerweise über den Fachhandel abgewickelt.
Bespoke Battery Concept: OEMs Welcome!
Doch im Moment konzentriert man sich intern immer mehr auf das OEM-Business. Seit 2020 entwickelt man das Bespoke Battery Concept für »maßgeschneiderte« Batterien für den OEM-Kunden, intern wurde die Entwicklung und Fertigung dafür ausgebaut. »Wenn man die einzelnen Expertisen zusammenzählt, haben wir 70 Jahre Erfahrung in der Akku-Branche«, rechnet Bär. CTO Marcel Wilke etwa, der schon 25 Jahre in Akku-Unternehmen arbeitet, hat ein Team für die Hardware-Entwicklung aufgestellt. Für OEMs bieten die Haibacher zwei Möglichkeiten. Die erste ist eine eigene Lösung, in der der Akku individuell auf den Kunden zugeschnitten ist und komplett von Akku Vision entwickelt und gebaut wird. Bei der zweiten geht es um einen Mix. Das Design des Gehäuses ist individuell entwickelt und ausgeführt, die technischen Lösungen kommen aus dem Portfolio von Akku Vision.
Die automatische Verschweißung der Kontakte sorgt für hohe Qualität der Batterie.
Die Bestückung mit Schablonen macht Fehler praktisch unmöglich.
Fortschritt: flexibler Verbinder für Intube-Batterien.
Seit 2022 stellt Akku Vision für Oli aus Italien einen Inframe-Akku her, und auch für Beryl, Leihradanbieter mit eigenem System in Großbritannien, liefert das Unternehmen seit letztem Jahr Energieträger für die Rahmenintegration. Auch die Gehäuse werden selbst entwickelt, die Konstruktion sitzt in Haibach. Dort surren mehrere 3D-Drucker vor sich hin und erstellen Prototypen für die Gehäuse neuer Kunden.
Software aus eigener Entwicklung
»Die Software ist bei der hochwertigen Batterie das Ein und Alles«, bekräftigt Schüßler. In der Entwicklungsabteilung für diesen Bereich arbeiten sechs Spezialisten. Sie kümmern sich um das Batteriemanagementsystem, die Kommunikation zwischen Motor und Batterie, die Traceability und alle anderen Aspekte der Steuerung. Traceability etwa bedeutet, dass alle Daten des jeweiligen Produkts in eine Datenbank auf der Platine eingeschrieben sind. Diese Daten werden den Kunden, also dem Fachhandel, zur Verfügung gestellt, der Weg der Batterie und alles, was in ihr passiert, ist nachverfolgbar. Auch die Abschaltwerte, sollte die Batterie zu heiß werden oder ein anderes Problem auftreten, werden von der Software definiert. »Auch dieses System wurde von Akku Vision selbst entwickelt«, so Schüßler. Schließlich muss man nicht nur die Normen wie die ISO 9001:2015 einhalten. Dazu kommt auch die Functional Safety. Was passiert, wenn jemand den Akku kurzschließt oder ein falsches Ladegerät anschließt? Nichts, denn das BMS muss reagieren und einen Schadensfall verhindern, etwa durch Ausschalten des Akkus oder Stilllegen betroffener Zellen. Akku Vision steht mit einer zweijährigen Garantie für die dauerhafte Leistung des Produkts gerade.
Fast wie Lego, nur Hightech
Die schon angesprochene Produktionsabteilung macht einen kleinen Teil einer separaten Halle aus. Aus den ESD-ausgestatteten Lagern nebenan kommen, bereits pro Auftrag kommissioniert, die Einzelteile. Hier werden dann zunächst Zellen anhand von Schablonen in Zellträger eingesetzt, die Zellverbinder, also die Kontaktwege zwischen den einzelnen Zellen, werden danach in einem komplexen Schweißvorgang verbunden. Dann wird die Einheit mit dem Batterie-Management-System verheiratet und schließlich bekommt der Akku sein Gehäuse mit dem E-Bike-Vision-Label, wenn es ein Ersatzakku für den Aftermarket ist. An einer End-of-Line-Kontrolle wird jeder Akku ausgiebig getestet. So weit der stark vereinfachte Ablauf. Dabei ist zum Beispiel »die Königsdisziplin«, wie Benjamin Hösel das automatische Schweißen der Verbinder auf die Zellen nennt, noch gar nicht beschrieben. »Das ist ein enormer Fortschritt und ein absoluter Zugewinn an Sicherheit«, so Hösel. Das händische Schweißen der Verbinder, das heute oft noch üblich ist, kann bei Weitem nicht die Genauigkeit liefern wie dieser Vorgang.
»Software ist bei hochwertigen Batterien das Ein und Alles.«Florian Schüßler, CPO
Auch sonst ist die technische Entwicklung selbst für Laien zu sehen. Die Flexfolie etwa löst Mittelabgriffe ab, auch Balancing-Kabel genannt, die vorher die Einzelzellspannung mit dem BMS verbunden haben. »Die Umsatzzahlen haben sich in den letzten Jahren regelmäßig verdoppelt«, so Bär. Und natürlich hat die Pandemie über das gesteigerte Interesse am E-Bike kräftig mitgeholfen. Derzeit werden hier bis zu 270.000 Akkus im Jahr produziert. Bis 2025 will man auf satte 1,7 Millionen aufstocken. Dann deutlich mehr automatisiert sein. »Bei der derzeitigen Produktionsmenge ist die weitere Automation noch nicht wirtschaftlich«, erklärt Benjamin Hösel. Bald ist das anders. Dann wird man nochmals deutlich Personal aufstocken.
Der Händler als Service-Ansprechpartner
Die Service-Abteilung ist klein, umfasst gerade einmal drei Mitarbeiterinnen und den Leiter Heiko Proske. Ihn kontaktieren die Händler im Falle einer Service-Anfrage. »Wir haben 0,65 Prozent Rücklaufquote«, erklärt er. Der Wert zeigt, dass die Kunden mit der Qualität der Akkus zufrieden sein dürften. »Die Regelung ist, dass die Geräte innerhalb von 72 Stunden wieder raus sein sollen. Meist geht es aber schneller.« In einem kleinen Labor werden die Akkus wie beim Radfahren elektrisch belastet. Messgeräte prüfen dann alle Parameter und vergleichen mit der Soll-Norm. So sind Fehler schnell gefunden und oft auch entsprechend zügig behoben.
»Falls der Schaden eine Reparatur unwirtschaftlich macht, bieten wir einen Tausch an«, so Proske. Beschädigte Gehäuse werden gegen 100 Euro ersetzt, sofern der Akku technisch in Ordnung ist. Neben der regulären 24-monatigen Gewährleistung bietet die Akku Vision ihren Kunden eine 24-monatige Garantie und gegen einen Aufpreis auch ein Jahr Verlängerung an.
Gute Perspektiven
Ganz wichtig ist dem Unternehmen, nicht mit Refurbished-Unternehmen gleichgesetzt zu werden. Dort würden oft nur schadhafte Zellen einer älteren Batterie ausgetauscht. »Eigentlich ist das rechtlich ohnehin schon mehr als ein Graubereich«, so Schüßler. Kein Service, oft zweifelhafte Qualität und Sicherheit und ein dickes Fragezeichen, was im Schadensfall passiert, das ist das Gegenteil dessen, wofür Akku Vision stehen will. Eine Frage, die Handel und Verbraucher trotzdem interessiert, ist die nach den Garantie- und Gewährleistungsansprüchen, die sich aus dem Zusammenspiel mit den E-Bike-Antrieben von Herstellern ergeben, die teilweise explizit Wert darauf legen, nur mit Originalakkus betrieben zu werden. »Wir können keine Aussage treffen, wie unsere Mitbewerber das Thema Garantie behandeln. Dies ist für unsere Ersatzakkus der Marke E-Bike Vision auch nicht wirklich relevant.«
»Unsere Produkte kommen typischerweise dann zum Einsatz, wenn der Kunde sein E-Bike bereits über einen längeren Zeitraum nutzt oder der originale Akku nicht mehr die gewünschte Reichweite bietet«, erklärt Geschäftsführer Maiberger. In der Regel sind dann diesbezügliche Ansprüche nicht mehr vorhanden. »Dann bekommt der Kunde bei uns einen Ersatzakku mit mehr Kapazität und damit auch mehr Reichweite. Soll ein Zweitakku her, dann bieten wir auch hier eine kostengünstige Alternative.«
Mittlerweile gibt es hier auch Produkte jenseits der E-Bike-Batterie. In Haibach wurde ein Batterie-Testgerät für die eigenen Akkus entwickelt. Es soll Fehlerdiagnose und Service für den Händler leichter machen, ist zu verschiedenen Modellen kompatibel und entstand aus der internen Arbeit. Und mit Fusione geht man erstmals ganz weg vom E-Bike. Dieser Batterietyp wird in gewerblichen Lastenfahrzeugen und unterschiedlichen Mikromobilen eingesetzt. Langfristig will man sich deutlich mehr auch in diese Richtung orientieren. Aber »bislang hatten wir einfach nicht die Zeit, uns darum zu kümmern«, so Bär. //
Verknüpfte Firmen abonnieren
für unsere Abonnenten sichtbar.